Production photos
Process
Much of the design process for this show developed out of creating looks around significant stage pictures, and then interpolating out into the rest of their scene. An early concept of an opening moment picture was fun to toy with as if it was a painting that needed filling in, and we experimented with color and texture in the early stages of design development. The design evolved over the entire production process, starting in early blocking rehearsals and ending once the curtain rose on our performance at state finals in Boston at the Back Bay Events Center.
Glowing Bottle practicals
One of my projects was adding electrified bottles to a canopy net. I used colored, plastic bottles with fairy lights inside to be powered externally by a 5V DMX decoder. The entire scenic setup had to be assembled on stage in 5 minutes to comply with competition regulation. This meant all wiring in the canopy had to survive being folded up and transported many times, quickly.
The first iteration of the bottles began smoking during our competition performance and a revised prop was constructed.
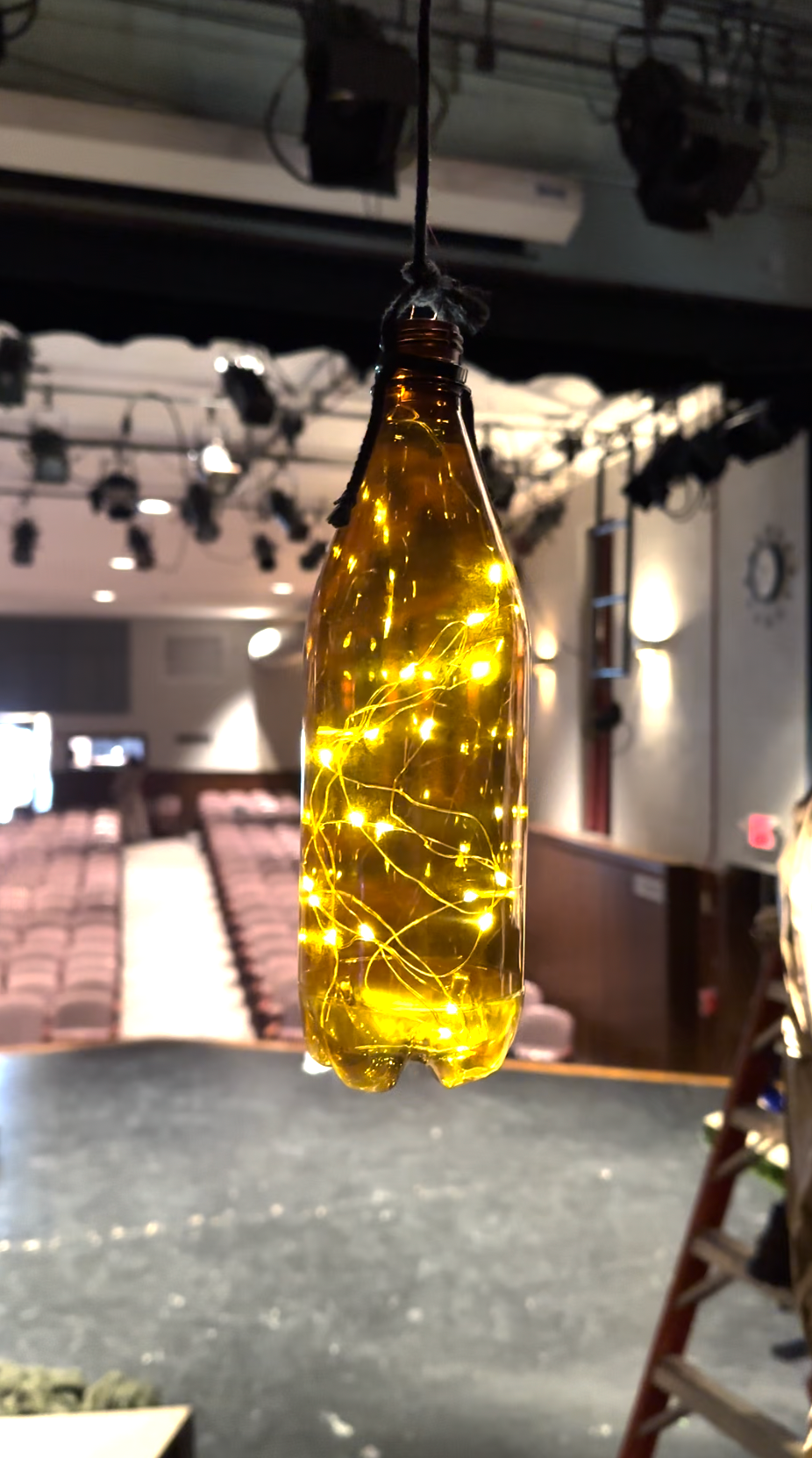
First iteration of light up bottles
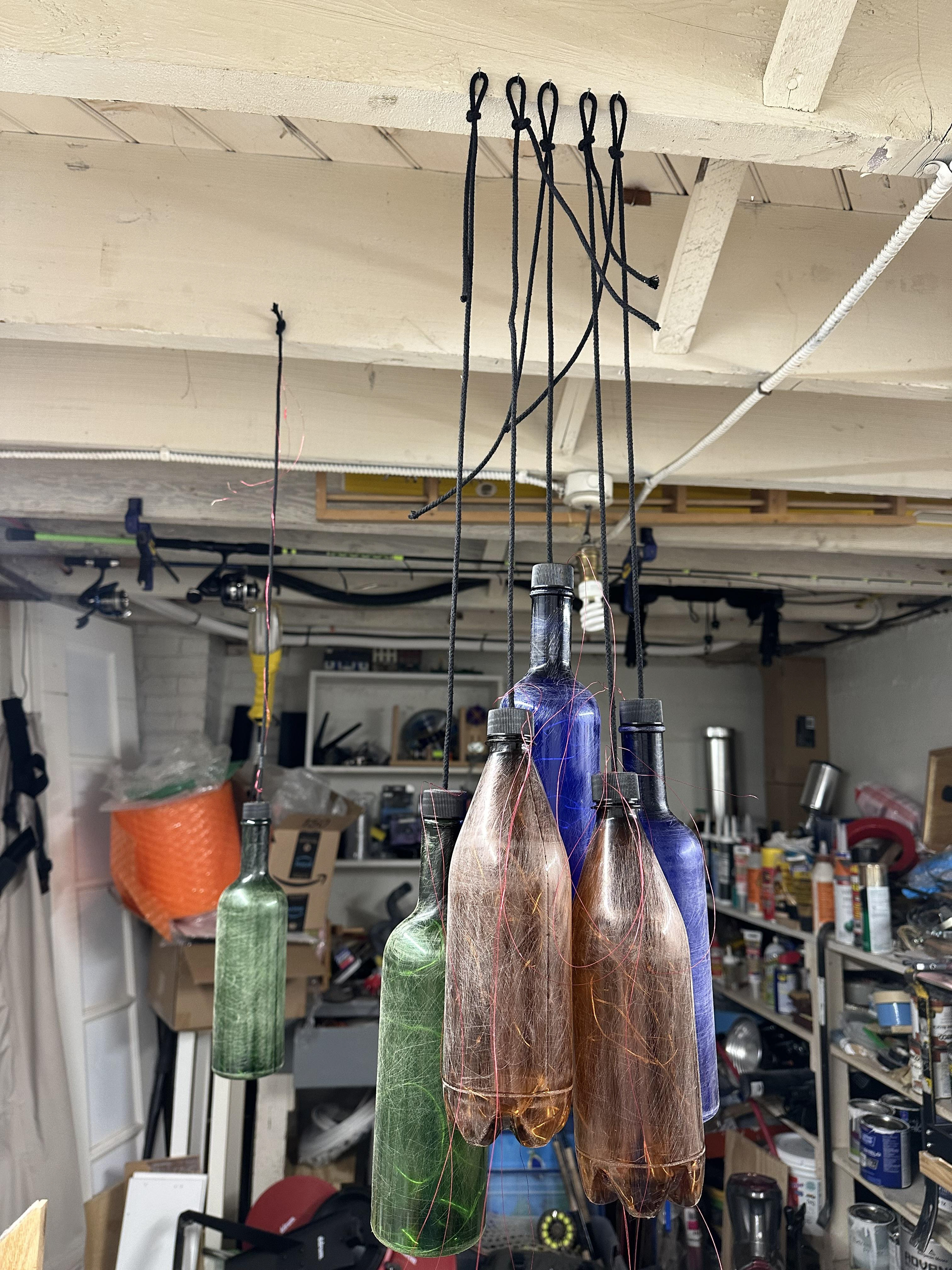
The revision 2 bottles were capped and all connections were soldered and heat shrunk to prevent any shorts. The bottles were also weathered with sandpaper to diffuse the glowing lights inside.
The bottles were attached to the canopy permanently and all power network wires were securely zip tied into the woven grid with enough slack to allow folding and stretching. If I had more time and resources, I would've used more robust wires that camouflaged better and disconnect-able bottles to transport separately.
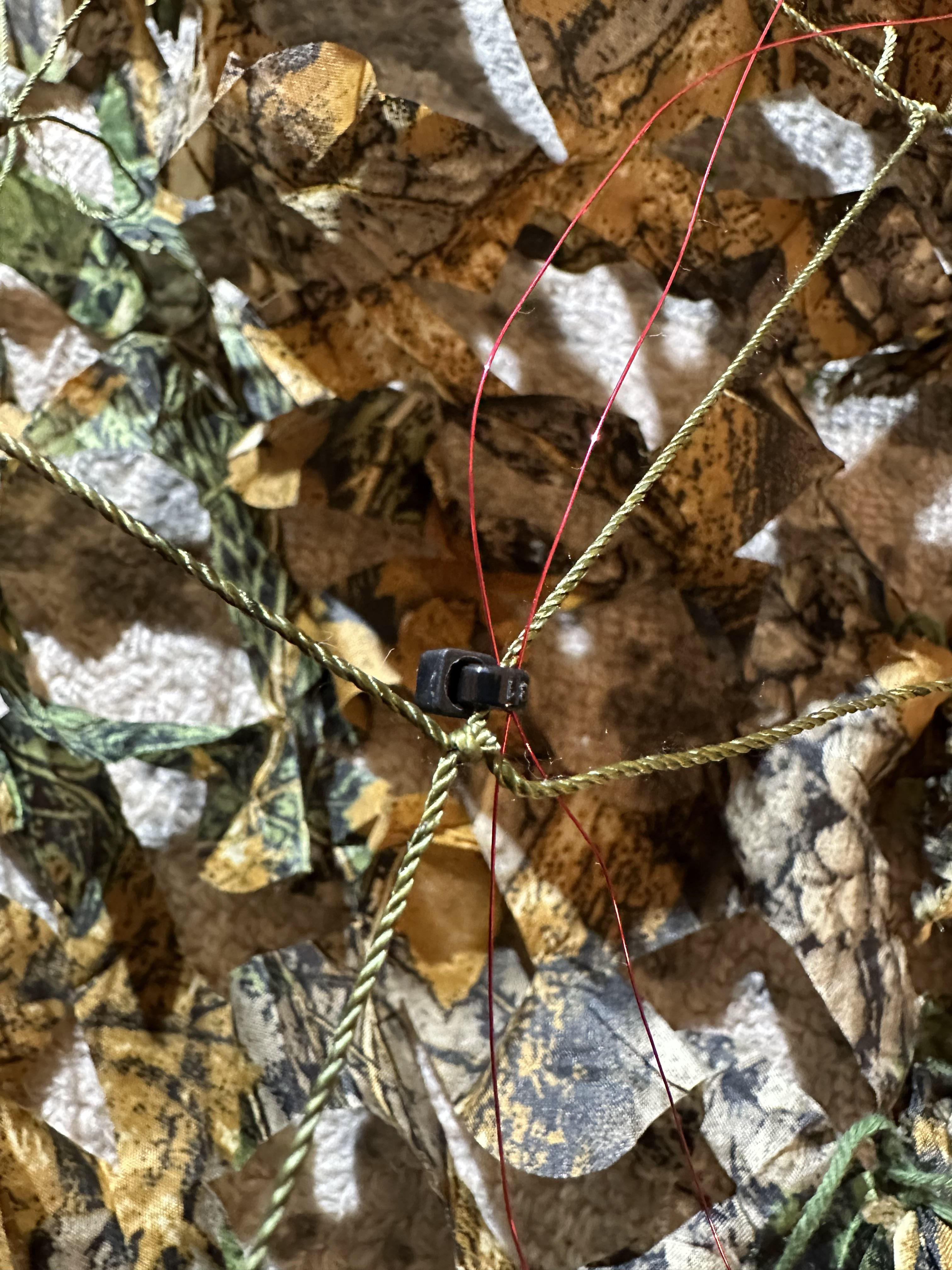
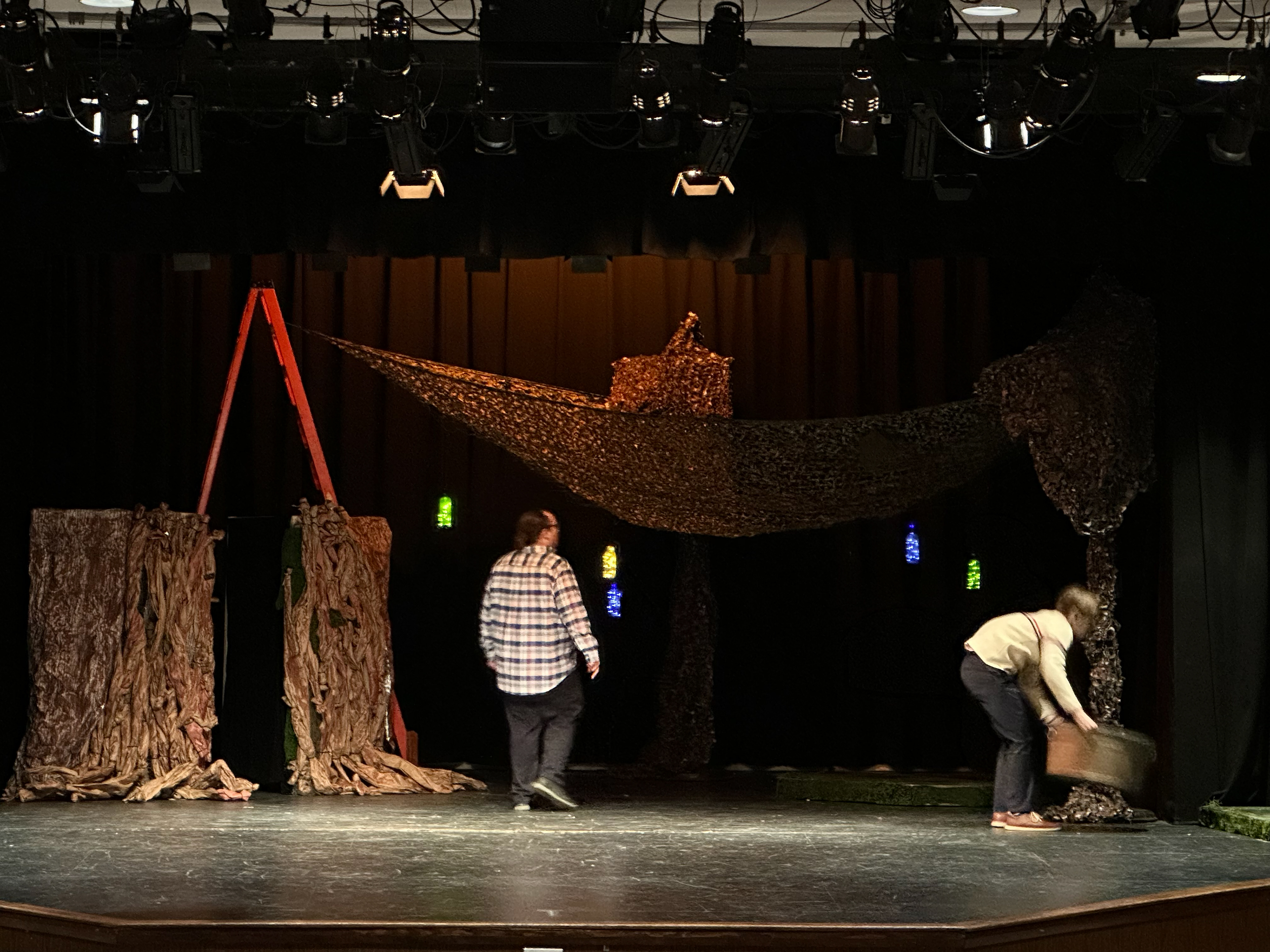
The final result!